Am Anfang
Dieses Thema war seit der Gründung von Combelle Gegenstand vieler interner Debatten, da ich nachhaltige Praktiken in den Mittelpunkt der Werte der Marke stellen wollte.
Daher schien die lokale Produktion die naheliegende Wahl zu sein.
Das Geschäft begann mit der Suche nach einer geeigneten Strickwerkstatt. Ich begann im Umkreis von 80 Kilometern und fand viele, aber keine passte, sodass ich bald weiter in die Ferne suchte. Gleichzeitig begann ich, lokale Garnmessen zu besuchen und mir eine Garnsammlung im Designstudio aufzubauen.
Nach endlosem Klinkenputzen und der Hilfe eines befreundeten Agenten begann ich, mich mit Fabrikbesitzern zu treffen. Allerdings wurde schnell klar, dass die Komplexität der Designs gegen mich arbeitete, denn sie blätterten mit großen Augen durch die Designpakete und sagten mir, ich müsse vereinfachen, entfernen, eliminieren.
Es dauerte sechs Monate, bis sich endlich eine Fabrik bereit erklärte, mit mir zusammenzuarbeiten (ironischerweise war es auch die erste Fabrik, die ich je kontaktiert hatte. Sie gab nach, nachdem ich beschlossen hatte, es noch einen letzten Versuch wert zu sein). Es schien wie ein Traum, ich konnte sie mit dem Auto erreichen (eine kurze Fahrt über sanfte Hügel in einem Fiat 500 von 1966, sehr instagrammable!).

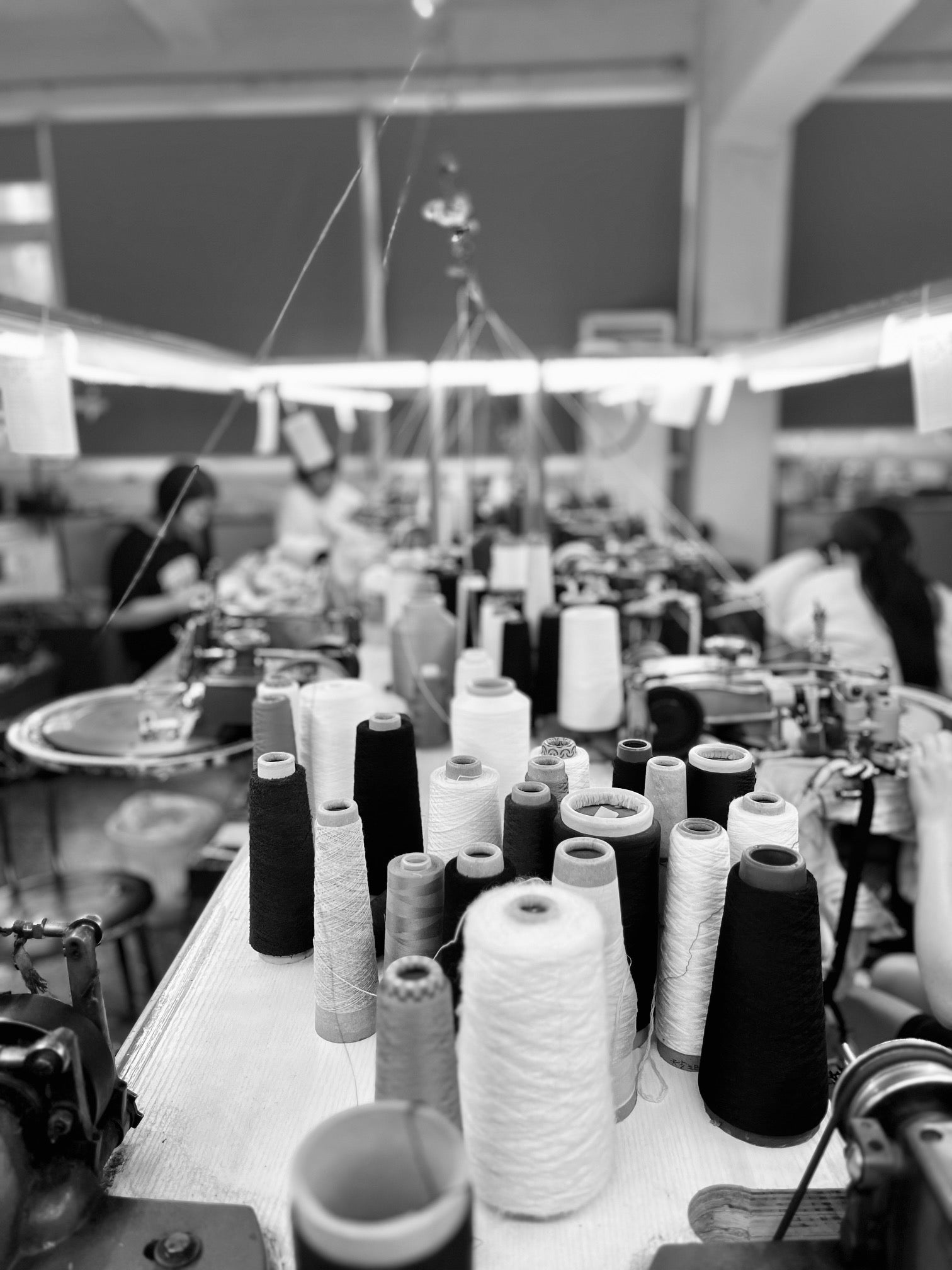
Ein Fehlstart
Die Entwicklung der fünf Modelle der Launch-Kollektion begann. Rückblickend war jedoch von Anfang an klar, dass die Strickqualität und die technische Umsetzung der Designs nicht meinen Anforderungen entsprachen. Die Strickkonstruktion war schwer, und die luxuriöse Wirkung des wunderschönen Viskose-Seidengarns schien irgendwie verloren gegangen zu sein. Verschiedene Verarbeitungen konnten nicht angeboten werden, die Streifenwinkel konnten nicht verbessert werden, und die verfügbare Technologie war begrenzt. Es dauerte fünf Monate, bis mir jeweils ein Muster – die erste Version – zur Begutachtung vorlag, und in diesem Moment wusste ich tief im Inneren, dass ich versuchte, etwas zu erzwingen, was nie zum bestmöglichen Produkt für meine Kunden führen würde.
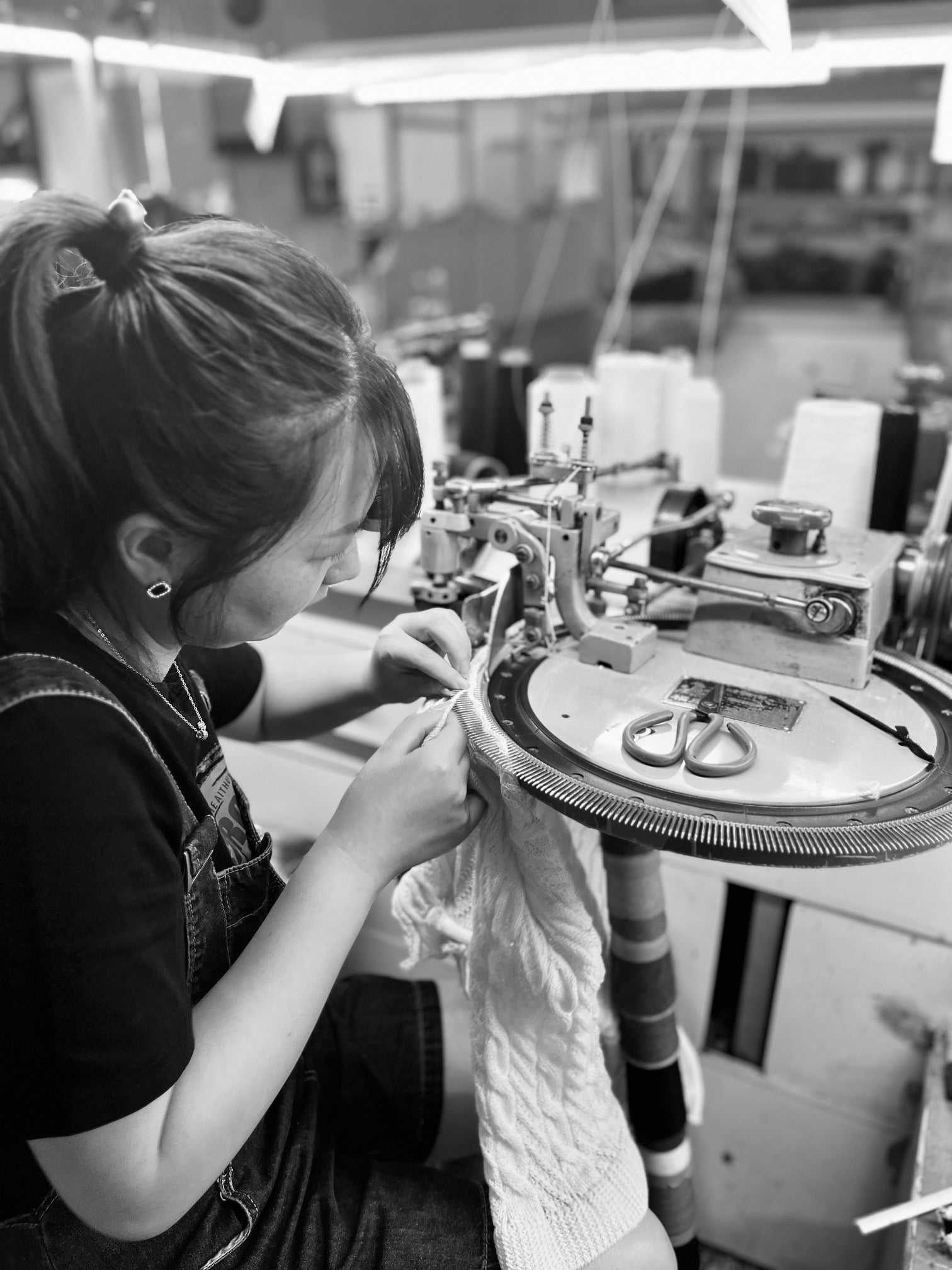
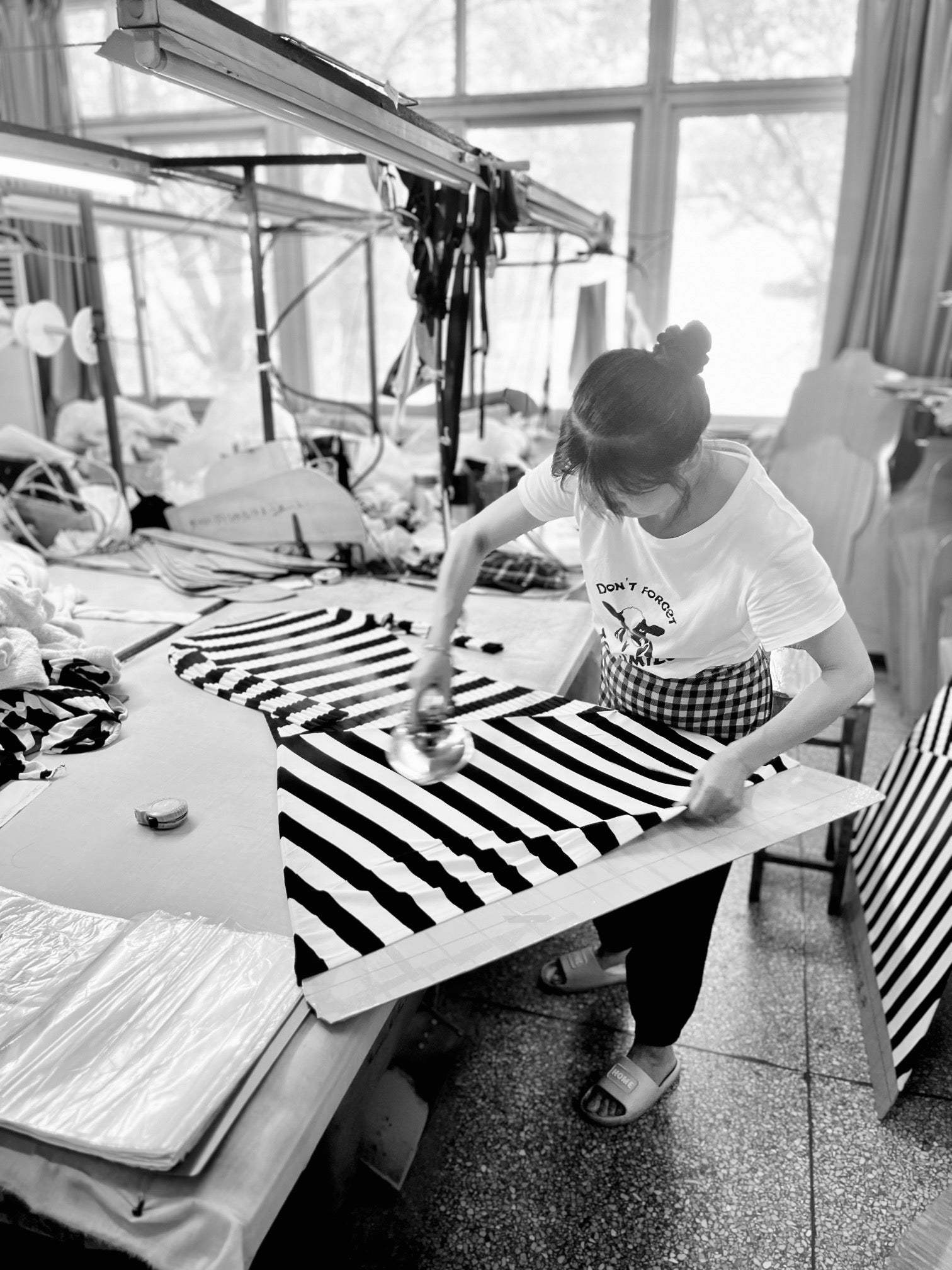
Ein anderer Ansatz
Im vergangenen Sommer – während ich noch damit beschäftigt war, Fabriken in meiner Nähe zu besuchen – besuchte ich eine Messe für nachhaltige Beschaffung in London. Ich hatte viele potenziell geeignete Kontakte zu Herstellern geknüpft und begann mit der Probenahme. Dazu schickte ich jedem Hersteller das gleiche Design, um seine Geschwindigkeit, seine Verarbeitung und seine Entwicklungskommunikation zu testen. Viele ließ ich fallen, bevor ich ein Muster sehen konnte, und am Ende kam nur einer durch. Und sie überzeugten mit Bravour.
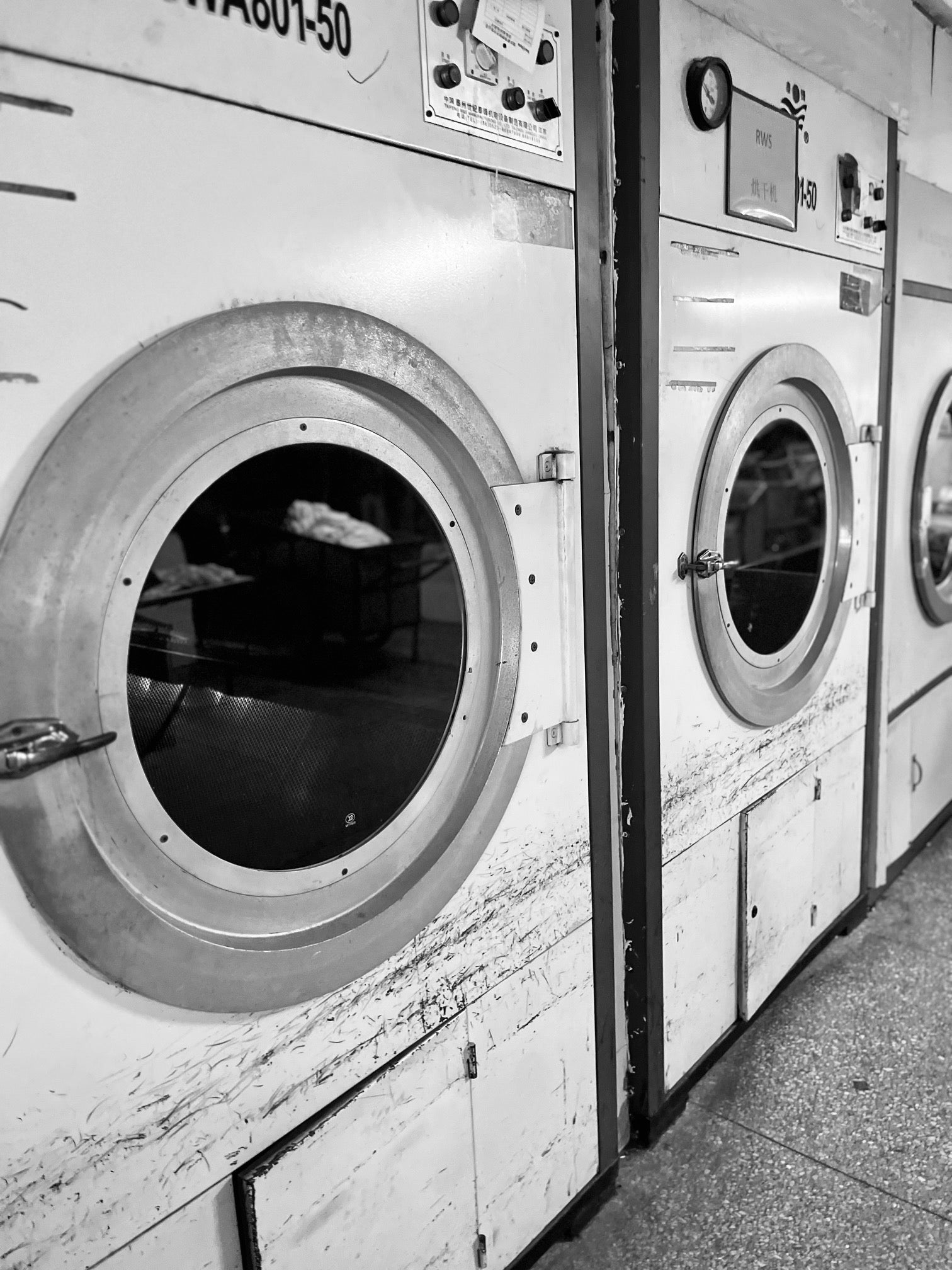
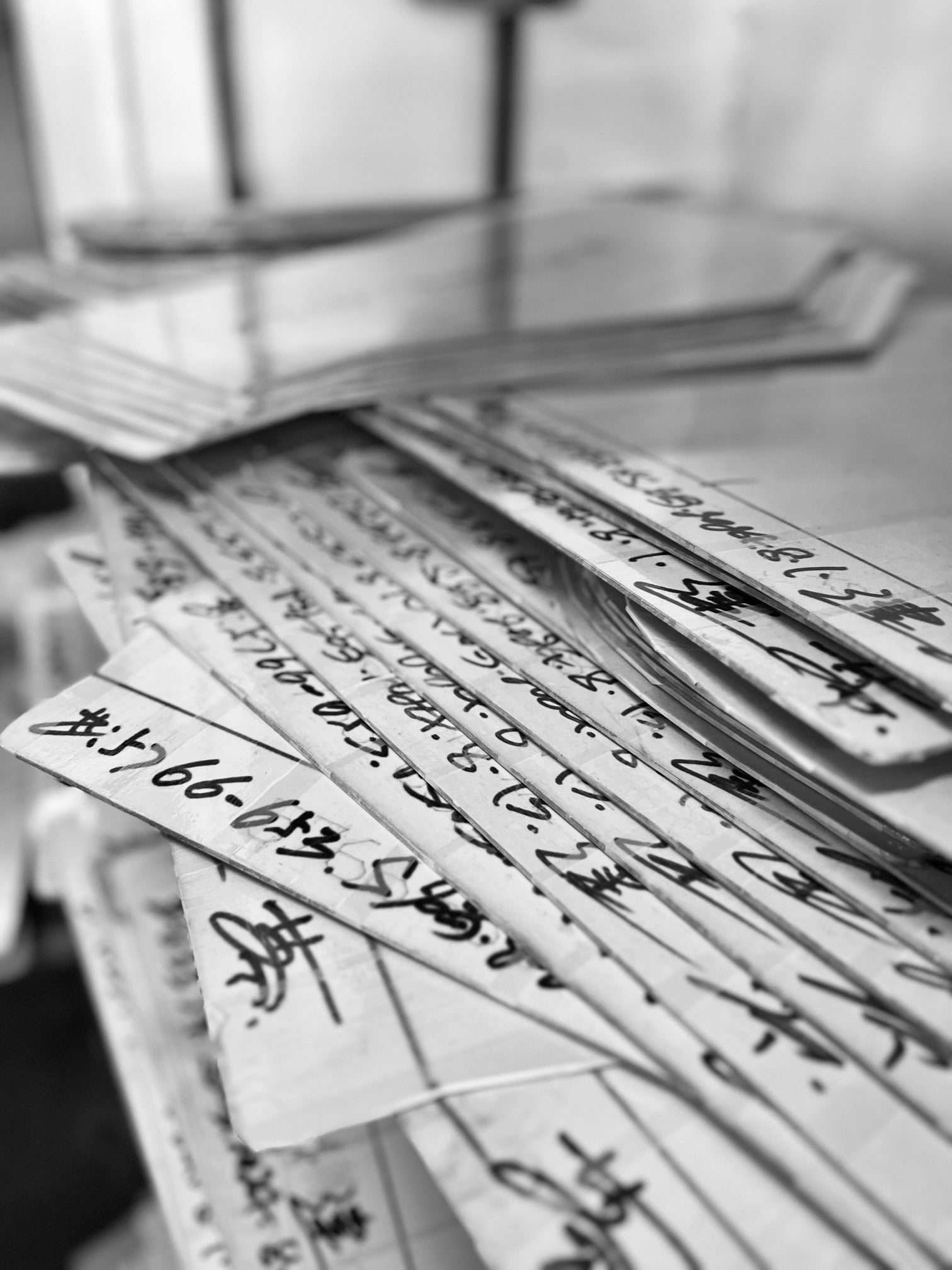
Ich folge meiner Intuition
Es handelte sich um eine sehr etablierte Strickwarenfabrik etwas landeinwärts von Shanghai. SMETA-geprüft, RWS-, OCS- und RCS-zertifiziert und mit soliden Umwelt- und Biodiversitätsrichtlinien ausgestattet, war die geografische Entfernung meiner Meinung nach der einzige verbleibende Nachteil. Selbst von der europäischen Produktion war dies weit entfernt. Ich kann jedoch nicht leugnen, dass ich nach sechs Jahren enger Zusammenarbeit mit zwei Fabriken weiter südlich in Guangzhou für mein vorheriges Unternehmen ein wenig in die chinesische Produktion verliebt war. Ich bin mir der negativen Assoziation mit „Made in China“ nur allzu bewusst, doch meine persönlichen Erfahrungen waren unvergesslich positiv, und lebenslange Freundschaften sind aus diesen Jahren geblieben. Keine der Fabriken produzierte Strickwaren (obwohl eine anbot, zu investieren und die Produktion für mich zu übernehmen, als ich ihnen von meinen Plänen erzählte, eine Marke zu gründen … Sie werden eine etwas andere Einstellung bemerken als die, die ich näher zu Hause erlebt hatte). Verträge hatten sich in reines Vertrauen aufgelöst, und innerhalb kürzester Zeit hatte sich eine Synchronizität von Arbeitspraktiken und -prozessen entwickelt. Sie hatten eine unerschütterliche Arbeitsmoral, waren reaktionsschnell, transparent, effizient und unglaublich gut organisiert.
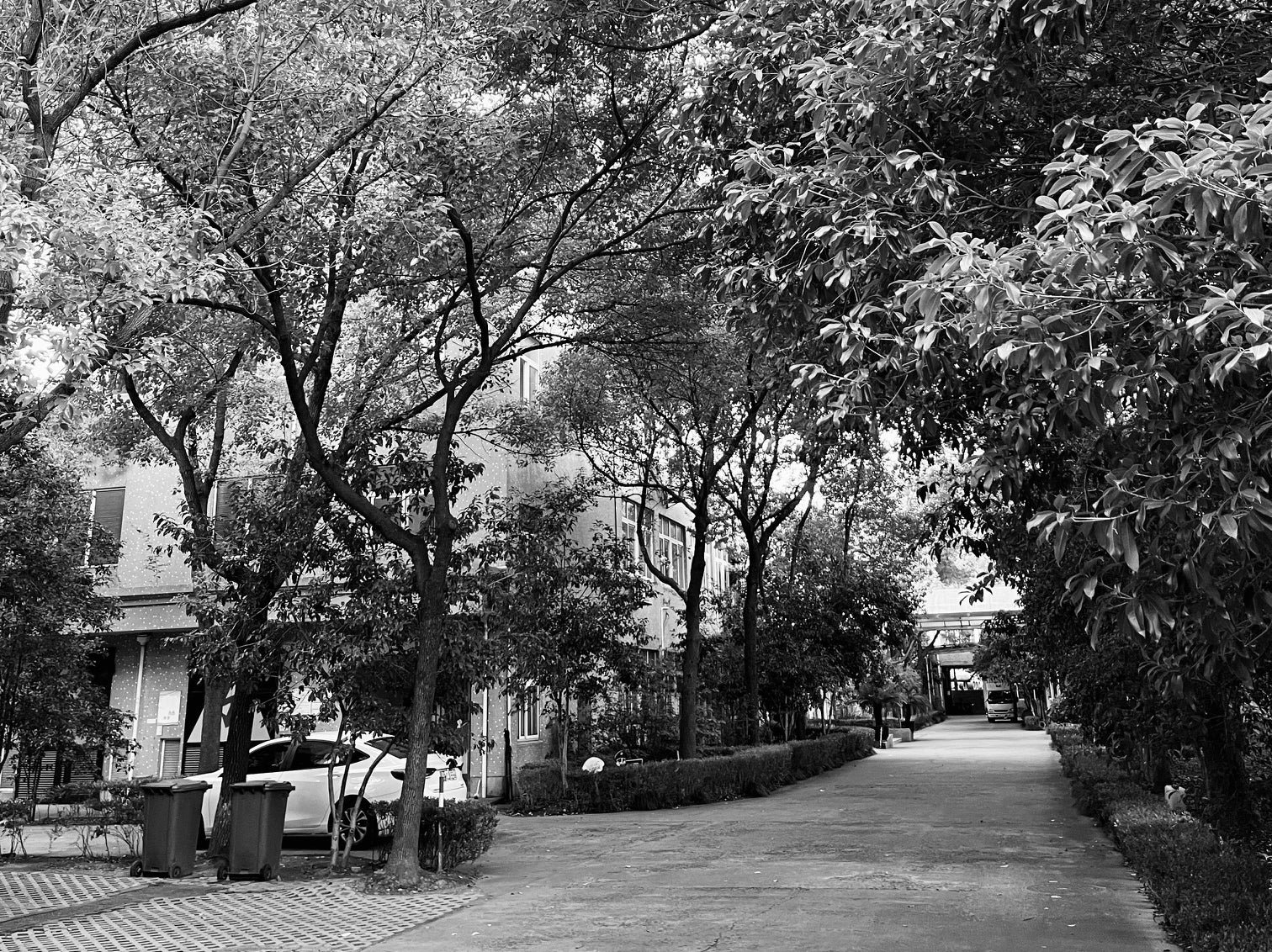
Unbestreitbare technische Expertise
Charing, mein Ansprechpartner in Shanghai, benötigte drei Wochen, um das Muster nach dem gesendeten Entwurf anzufertigen. Verfahren zur Bewältigung der Konstruktionsprobleme wurden per E-Mail besprochen, und es wurden inspirierende Lösungen vorgeschlagen. Einige der Veredelungstechniken, die die lokale Fabrik nicht reproduzieren konnte, wurden auf dieses Muster angewendet, da ich es schon lange vor Beginn des langsamen Musterprozesses in den Händen hielt. Tatsächlich war das Testmuster, das Charing mir schickte, perfekt. Es ließ sich vom ersten Muster an versiegeln, was angesichts der technischen Komplexität (es handelte sich um das Alix-Oberteil, wie Sie es kennen) an ein Wunder grenzte.